Inventory cost refers to the expenses associated with acquiring, storing, and maintaining inventory within a business. It includes various components, such as the cost of purchasing or producing inventory, carrying costs, and any other costs related to inventory management. Reducing inventory costs in logistics is a common objective for many businesses as it can improve cash flow and increase overall profitability. Here are several strategies you can implement to reduce it :
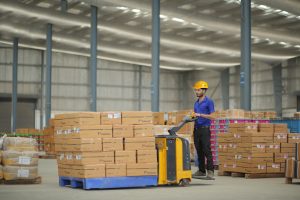
-
Demand forecasting :- Accurate demand forecasting helps you anticipate customer demand and avoid excessive stock. Analyze historical data, market trends and customer behaviour to make informed predictions about future demand.
-
Supplier management :- Establish strong relationships with reliable suppliers who can provide competitive pricing, favorable terms, and timely deliveries. Negotiate better pricing, volume discounts and explore options for consignment or vendor-managed inventory (VMI) arrangements.
-
Just-in-time (JIT) inventory: Adopt the JIT approach to minimize inventory carrying costs. Order and receive inventory only when needed, reducing the need for excessive stockpiling and associated holding costs.
Just-in-Time 4) Optimize order quantities: Use economic order quantity (EOQ) calculations to determine the ideal order quantity that minimizes total inventory cost. Consider factors such as carrying costs, ordering costs and stock-out costs when calculating EOQ.
5) Inventory classification: Implement an ABC analysis to categorize your inventory based on value or sales volume. Focus on optimizing the management of high-value items or fast-moving products while considering alternative approaches for low-value or slow-moving items.6) Efficient storage and layout: Organize your warehouse or storage area to maximize space utilization. Implement efficient storage systems such as vertical racking, labeling, and inventory tracking technologies to minimize the risk of overstocking or lost inventory.
7) Regular inventory audits: Conduct regular inventory audits to identify and address issues such as stock obsolescence, shrinkage, or inaccuracies. Implement robust inventory control systems, such as barcode scanning or radio-frequency identification (RFID), to improve accuracy and visibility.
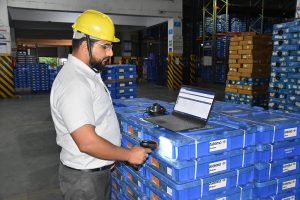
8) Collaboration and partnerships: Explore partnerships or collaborative relationships with suppliers, distributors, or retailers to streamline inventory management. Sharing sales data, forecasts and inventory information can help reduce stock-outs and improve overall supply chain efficiency.
9) Just-in-case inventory: Review and optimize safety stock levels by considering lead times, demand variability and supplier reliability. Avoid excessive safety stock that can tie up capital and increase carrying costs.
10) Continuous improvement: Regularly evaluate and refine your inventory management processes. Look for opportunities to eliminate waste, reduce lead times, and improve overall efficiency. Embrace technologies such as inventory management software, demand planning tools and automated order processing systems.
By implementing these strategies, you can effectively reduce holding cost while maintaining adequate stock levels to meet customer demand. Keep in mind that the optimal approach may vary depending on your industry, business model, and specific circumstances.
The primary elements of inventory cost are as follows: –
1) Purchase Cost :- This is the direct cost of acquiring inventory from suppliers or manufacturers. It includes the price of the goods, transportation costs, import duties & any other expenses directly attributable to the purchase.
2) Carrying Costs :- These are the expenses incurred to store and maintain inventory. Carrying costs typically include warehousing expenses (e.g., rent, utilities, insurance), security, inventory tracking systems and labour costs associated with handling and managing inventory.
3) Holding Costs :-Holding costs are the expenses incurred due to keeping inventory on hand for an extended period. This can include costs related to obsolescence, deterioration, damage or theft of inventory. It may also encompass the opportunity cost of tying up capital in inventory rather than investing it elsewhere.
4) Ordering Costs :- Ordering costs are the expenses associated with placing and receiving orders for inventory. This includes activities such as order processing, paperwork, communication and transportation costs for inbound shipments.
5) Stockout Costs :- These costs arise when inventory is insufficient to meet customer demand. Stockout costs may include lost sales, customer dissatisfaction, rush orders, expedited shipping charges and potential damage to the business’s reputation.
6) Financing Costs :- Financing costs are applicable if the business uses loans or other forms of financing to acquire inventory. These costs include interest payments and fees associated with borrowing money to purchase inventory.
Calculating inventory cost accurately is crucial for businesses to understand the financial impact of their inventory management. By analyzing this cost, a company can make informed decisions regarding pricing, purchasing, reordering and inventory control strategies to optimize profitability and maintain adequate stock levels.
